Industry 4.0: Digitalising manufacturing
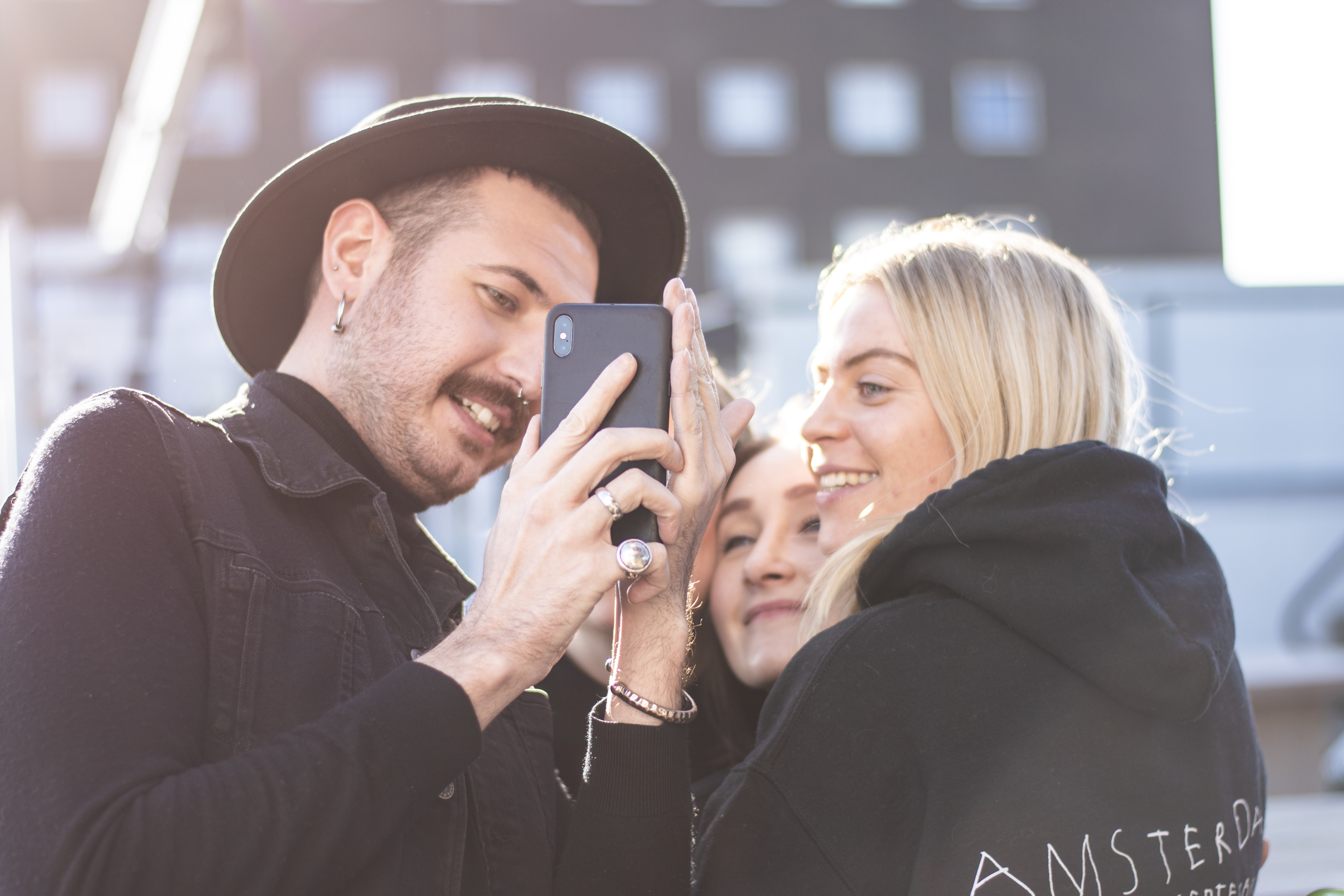
Grocery retailer Sainsbury’s is the latest business to announce its investment in the digitalisation of its operations, with the integration of an AI supply chain management system. Used in key areas such as demand forecasting, replenishment, space, range, warehouse, and labour management, the platform uses autonomous self-learning, combined with machine learning capabilities, to reduce man hours spent on key operational processes.
There’s a dual benefit to this investment; Sainsbury’s will reduce operational costs and waste, while customers should feel the benefit of fully stocked shelves. Being able to monitor, respond, predict and prevent supply chain disruptions has the potential to revolutionise the retailer’s supply chain.
Digitalising operational processes is a natural step forward in the evolution of a company’s digital transformation. The manufacturing sector has already gone through a major step forward; it wasn’t too long ago that paper drawings, 2D schematics and paper sign-offs were the norm, more recently replaced with digitised 3D CAD files, and cloud and tablet enabled docs. Rapid technology innovation has now reached a point where emerging technologies are now widely available.
Take machine learning and AI. Machine Learning has the ability to automate analysis, and detect patterns of data at a rate that would be impossible for humans to achieve. It can take data segmentation beyond simple keyword clusters, and opens up the opportunity to glean information from new data sources, such as audio, image and video. Apply this to your communication channels, and you can make vast time savings. For example, an AI chat-bot could alleviate pressure on your call centre, while providing timely, relevant answers to your clients’ queries. And it’s not as costly or complicated to implement as you may think. In addition, launching a ‘my account’ service could enable your clients to self-serve online and reduce telephone or email ordering, freeing up field sales teams to focus on new client acquisition, and your call centre to focus on solving any client issues.
Digitisation can also improve compliance and prevent bottlenecks. On a simple level, this can be indicating that every field on a form is mandatory and preventing submission until it’s fully complete. Hefty PDF manuals stored in a distant system that no one can find, let alone update, can be delivered via structured content management solution. Accessible, editable and compliance assured.
Smart manufacturing
Those manufacturers who are ahead of the curve are already looking to the next step in their digitalisation, embracing emerging technologies such as digital twinning, predictive maintenance, track-and-trace, and modular design. Technology innovation is now starting to enable smart manufacturing and smart factories, otherwise known as Industry 4.0.
Industry 4.0 focuses on connectivity, communication, data and automation. Big data, analytics and additive manufacturing have helped the industry to progress, and technology has now evolved to a point that can really take the sector to the next level of digitalisation.
Much like the Internet of Things (IoT), Smart Manufacturing connects factories digitally, with a central network that connects machines across all locations. This enables automation and the ability to learn processes independently, rapidly respond to change, and highlight quality issues.
On a practical level, machines have sensors integrated into the build. These sensors provide constant feedback in response to real-time data around things like maintenance requirements or production output. The machine-to-machine communication means that autonomous refinement takes place, and data is fed back into BI tools and dashboards for analysis.
This functionality can make your operations leaner, smarter, and more efficient.
Productivity, uptime and performance can increase, all while reducing overheads. We operate in a data economy and smart manufacturing is no exception. For the systems to work, real-time data fuels the learning-based decision process, at a speed far beyond the capabilities of a manual process.
For the laggards yet to adopt digitalisation, it won’t be long before their competitors have out-run them (if they haven’t done so already). One of the main issues of analog processes is scalability. Digitalisation makes data much easier to share, and for those global businesses operating ‘follow-the-sun’ manufacturing, this is imperative. As one plant closes for the day and one opens in another time zone, work can be handed over seamlessly with no downtime.
Cultural barriers to adoption
The benefits sound compelling and, according to a Microsoft study, over 50% of UK manufacturers are currently using the technology to some degree, whether that be smart digital assistants, voice recognition or machine learning. Although this stat is pretty impressive, there are key blockers to implementing smart operations further, and it’s not the technology.
Richard King, Head of Manufacturing and Resources for Microsoft UK, explains: “For manufacturers, there are broadly four stages of the AI journey: driving visibility and insights; creating predictability; automation and being prescriptive; and being cognitive and autonomous. Currently, organisations tend to be largely operating at stage one. So, to derive full value from AI, they need to start accelerating their progress. And that is as much about a cultural transformation as it is a technological one.”
So, how do manufacturers overcome the barriers to wider adoption? On one level, there’s a knowledge gap and lack of understanding of what AI solutions are; 54% of manufacturing leaders said they do not understand how their AI solutions arrive at conclusions, and 51% said they wouldn’t know what to do if they disagreed.
There’s also a major cultural hurdle to overcome. There is a general wariness among the manufacturing workforce that automating processes will result in a reduction in jobs. If leaders don’t fully understand the solutions, it’s difficult to build a culture where employees are empowered to re-skill and work alongside machines, as opposed to being threatened by them. For digitalisation of manufacturing processes to be successful, it needs by-in across the company, not just from the top.
More Insights?
View all InsightsQuestions?
VP of Marketing, EMEA